再流焊缺陷主要分为两大类,一类与冶金现象有关,包括冷焊、半润湿、不润湿、过多 的金属间化合物;另一类与异常的焊点有关,包括焊料量不足、桥接、锡球、锡珠、偏移、芯 吸、空洞、立碑等。
(1) 冷焊
冷焊即有不完全再流现象的焊点,通常表现为:颗粒状焊点,焊点形状不规则或焊料 合金不完全熔融,如图3.17所示。焊膏未熔融如果发生在特定部位,可能的原因有:元件 热容量过大,吸热多,温升速度较慢;未熔融焊料如果发生在任意地方,可能的原因有:焊 膏异常,如焊膏密封状态、保管温度、使用期限等有关问题,以及未用完的焊膏重复使用 等。一般来说,产生冷焊的原因有:①再流阶段加热不充分;②冷却阶段焊点发生扰动;③ 助焊剂能力不够;④焊料合金质量不合格。
(2) 半润湿(Dewetting)
半润湿即焊膏熔化时焊料浸润焊盘表面后发生收缩,焊料只覆盖焊盘部分区域,焊料 形状不规则,如图3.18所示。产生半润湿的原因有:①焊盘可焊性不良或不均匀;②焊盘 可焊性退化;③再流温度曲线不合理;④元器件引脚或PCB焊盘氧化或污染;⑤元器件与 熔融焊料接触时,焊膏在高温作用下的出气现象严重。
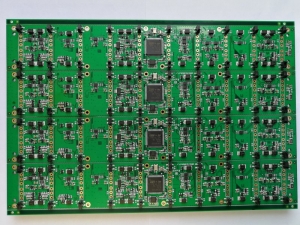
(3) 润湿不良
润湿不良即焊盘或元器件引脚上焊料的覆盖面积少于预期焊料覆盖面积,如图3.19 所示。通常是由于时间和温度比率不当造成的。焊膏内的活化剂大部分为有机酸,有机 酸随时间和温度的上升而退化。如果温度曲线太长或温度设置不当,焊盘或引脚的润湿 性极可能受到损害。产生不润湿的原因有:①焊膏湿润性差;②焊料合金质量不良;③助 焊剂活性不良;④再流温度曲线不合适;⑤焊盘或元器件引脚氧化或污染。
(4) 过多的金属间化合物
金属间化合物即在焊盘与熔融焊料或引脚与熔融焊料之间形成的新的金相组织,它 不是固液体,被称为中间相位或金属间化合物(IMC)o影响金属间化合物的因素有:焊接 过程中时间、温度设置,焊盘、引脚金属性能以及焊料合金的成分。减少过厚的IMC形成 的方法有:①在较低的温度和较短的时间下完成焊接,②锡铅比例适当的焊料;②采用阻 挡层金属,如镣。
(5) 焊料量不足
焊料量不足一般是因为印刷的焊膏偏少或者润湿不良。焊膏印刷量偏少跟焊膏的性 能有关,也与印刷机设定的参数紧密联系,另外相关的因素还有:模板开口是否被堵塞,开 口内壁光洁度、PCB板面光洁度、刮刀的硬度、印刷压力与速度是否适合,焊膏的滚动情 况(印刷时要求焊膏滚动)、焊料合金颗粒大小、焊膏黏度等。如果焊料量不足是由润湿性 造成的,则提高润湿性以增加焊料量。
(6) 桥接
桥接是指在不应当连接的地方连接上了,如图3.20所示。发生桥接的原因主要包括 焊料过多和引脚间距太小。发生桥接首先可能是在焊接之前焊膏已桥接,形成焊膏桥接 的原因有:①焊膏过多;②贴装压力过大;③冷塌。其次就是由于温度曲线的参数设置不 合理。对于细间距元件尤其是翼型引脚的元件很容易发生桥接。减少或消除桥接的方法 有:①使用较薄的模板,交错的孔图案,或减小开口尺寸;②减少贴装压力;③使用峰值温 度较低、升温速率较慢的温度曲线;④使用润湿速率较慢、溶剂含量较低的助焊剂。
(7) 锡球
锡球是指在再流焊过程中,熔融焊料离开了主要的焊接场所,凝固后不向主要焊接场 所聚集而形成不同尺寸的小球状颗粒的焊球,如图3.21所示。产生锡球的原因有:①印 刷后太久未过炉,焊膏发生氧化;②焊膏中溶剂的沸腾而引起焊料球飞散。减少或消除锡 球的方法包括从工艺与材料两方面入手。工艺方面:①提高焊盘和引脚的可焊性;②残留
在模板上的焊膏不能再度使用;③适当减少焊膏湿度;④避免焊接时间太长或太短,降低 升温速率;⑤印刷要严格对准;⑥减少模板开口尺寸;⑦使用惰性气体保护。材料方面:① 助焊剂的助焊活性、能力充分;②减少焊膏的氧化物、污染物含量;③提高焊膏金属含量; ④调整焊剂的成分,减少焊接过程中的飞溅物。
(8) 锡珠
锡珠指尺寸较大的锡球,它主要存在与片式电阻或电容的金属端周围,它是由焊剂的 挥发作用超过焊膏的内聚力造成的,如图3.22所示。焊剂挥发导致大量孤立焊膏的产 生,从而形成锡珠。减少或消除锡珠的方法同样可以从工艺与材料两方面入手。工艺方 面:①减少模板厚度、开口的尺寸;②改善开口形状,减少模板下面的焊膏;③降低预热温 度以及升温速率;④减少贴装压力;⑤调整温度曲线。材料方面:①使用较少塌陷(冷塌、 热塌)焊膏;②提高焊膏金属含量;③降低焊膏的氧化物;④使用较低活化温度的助焊剂。
(9) 偏移
偏移是指元件两端表面张力不平衡或其他原因造成的不处于焊盘对中位置并且偏移 量超过可接受的范围,如图3.23所示。产生偏移的原因有:①元器件两端焊盘设计不对 称;②元器件金属端宽度或面积太小;③引脚可焊性不良;④元器件贴偏。减少或消除偏 移的方法有工艺与设计方面:①提高贴装精度;②减少温升速率,尽量避免使用气相再流 焊;③增加焊盘的宽度和面积;④元器件两端焊盘设计均匀,增加元器件宽度和金属层的 面积;⑤减少焊膏厚度。材料方面:①使用出气较少的助焊剂;②使用润湿速率较低的助 焊剂。
(10) 芯吸
芯吸也叫抽芯,是指熔融焊料从焊盘开始沿引脚向上爬行,使得焊盘上只有少量甚至
完全没有焊料,如图3.24所示。芯吸产生的原因主要是引脚导热率过大,温升比焊盘快, 以致熔融焊料优先润湿引脚,可采用充分预热或底部加热的方法,减少芯吸的发生。通常 解决办法有工艺和设计方面:①使用的底部加热;②提高元器件引脚共面性;③适当增加 相对引脚的焊盘间距;④正确设计焊盘尺寸;⑤选择合适的加热方式。材料方面:①使用 较高黏度的焊膏;②使用较慢润湿速率、较高活化温度的助焊剂。
(11) 空洞
空洞即焊后焊点内部的孔洞,如图3.25所示。引起空洞的原因有:①焊膏凝固时收 缩;②焊接时,有气体排放;③焊剂的包覆;④峰值温度不够;⑤升温阶段温度速率过高。 此外,焊膏的组成与空洞密切相关,随着助焊剂活性的增加,空洞率随之减少。减少空洞 的方法有:①提高引脚、焊盘可焊性;②使用活性较高的助焊剂;③减少焊膏的氧化;④降 低预热温升速率从而促进助焊;⑤设置合适的峰值温度以及保持时间。
(12) 立碑
立碑指元器件的一端抬起,站立在另一端上,立碑也被称为“曼哈顿”现象,如图3.26 所示。立碑从原理上将是由元器件两端润湿力不平衡大于元件重力时引起的。产生润湿 力不平衡的原因有:①SMC / SMD两端焊料熔融时间不一致,焊盘面积,焊膏印刷量以 及贴片不精确等造成两端不对称而导致两端所受表面张力不平衡;②采用VPS再流焊接 时,容易产生浮力作用而导致片式元件直立。减少或消除立碑的方法有,工艺与设计方 面:①尽量采用圆形焊盘;②减少热量分布不均匀;③减少引脚、焊盘的污染和氧化;④减 少模板厚度,焊膏厚度;⑤提高元器件贴装精度;⑥降低温升速率;⑦提高印刷精度。材料 方面则采用润湿速率、出气速率较慢的助焊剂。
以上是怡泰SMT加工厂为您分享的关于smt加工时常见的再流焊缺陷分析的相关内容,如需SMT贴片加工服务,了解更多贴片加工知识,欢迎联系怡泰SMT加工厂。